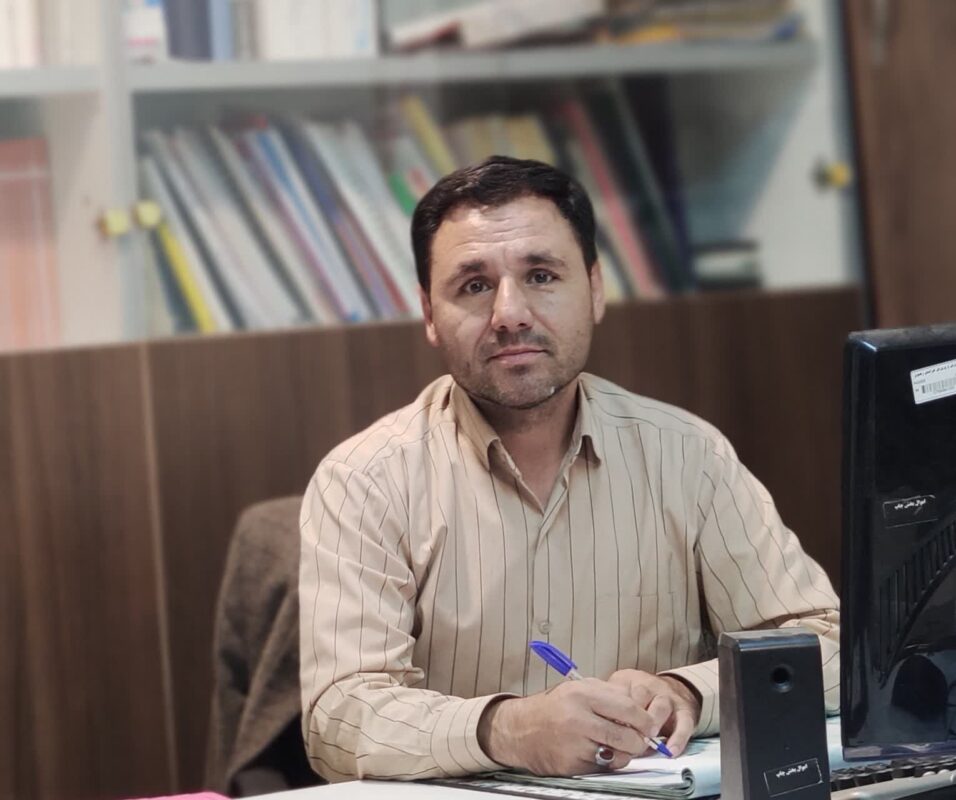
حمید زوزنی – مبنای چاپ افست تقابل و همراهی آب و مرکب است و تنظیم این دو عامل در حالی که یکی از ابتداییترین مراحل چاپ است، مهمترین بخش نیز به حساب میآید. همچنان که میتوان آن را به تیغ دولبهای تشبیه کرد که با اندک انحرافی میتواند سبب باطله شدن و هدر رفتن سرمایه و انرژی شود.
تنظیم آب و مرکب از جمله مسائلی است که در چاپخانههای ایران بیشتر به شکل تجربی و اکتسابی بوده و کمتر با جنبه علمی و تخصصی آن برخورد شده است.
این در حالی است که اگر اپراتور ماشین چاپ با هر یک از این دو عامل (آب و مرکب) به صورت علمی و تخصصی آشنا شده و جزئیات کار با آنها را بداند، در هر شرایطی میتواند به کیفیت نسبی در چاپ دست یابد.
سیستم آب باید طوری تعبیه شود که اپراتور بتواند در هر نقطه و سطح آبدوست، آب مورد نیاز را تغذیه کند تا امولسیون مناسبی به وجود آید. اگر قشر آب به صورت یکنواخت به روی پلیت انتقال پیدا نکند، مشکلات عدیدهای را برای چاپ به وجود میآورد که میتوان به پرکردگی (مرکب بیشتر از آب باشد) و یا بوری (آب بیشتر از مرکب باشد) اشاره کرد.
استفاده از داروی آب راهحلی است برای تنظیم پیاچ که استاندارد میزان مصرف آن در آب حدود ۲ تا ۳ درصد است. ولی ممکن است این میزان دارو با ماشین چاپ همخوانی نداشته و پس از اندازهگیری پیاچ محلول رطوبتدهی با وسیلهای به نام پیاچ متر، این میزان به ۴درصد هم افزایش یابد تا پیاچ آب برابر با عدد ۴ الی ۵ باشد.
برای داشتن یک کار چاپی خوب ۹ الی ۱۰ عامل مؤثر وجود دارد که یکی از آن ها آب است.
به طور کلی استفاده از آب در کار چاپ به این دلیل است که مانع رسیدن مرکب به مناطق غیرچاپی می شود. اما آب به تنهایی دارای یکسری کم و کاستیهایی است که نمیتواند این وظیفه را بهدرستی انجام دهد. بنابراین با افزودن داروی آب سعی در ارتقای عملکرد آن دارند.
یکی از عوامل استفاده از دارو، کاهش کشش سطحی آب است تا بتواند به صورت یکنواخت و کامل سطح پلیت را بپوشاند. از آن گذشته به دلیل سرعت بالای ماشین چاپ و گرمای ایجاد شده در حین کار، آب به سرعت تبخیر میشود و نمیتواند مانع رسیدن مرکب به سطح غیرچاپی شود. در عین حال مرکب ویسکوزیته (گرانروی) خود را از دست داده و زمانی که شل شد راحتتر وارد آب میشود. با افزودن الکل علاوه بر کاهش کشش سطحی آب، دمای آن را میتوان در حد مطلوب و به صورت ثابت نگه داشت.
در ادامه مطالب گذشته در این شماره به تشریح ویژگیهای الکل در چاپ و آشنایی با کنداکتیویته(هدایت الکتریکی) و سختی آب و نقش آنها در کیفیت چاپ میپردازیم که مطمئناً اطلاعات جالب و مفیدی در اختیارتان قرار خواهد داد:
کاهشدهنده کشش سطحی
دومین خاصیت که باید یک داروی آب داشته باشد، خاصیت کاهنده کشش سطحی است.
اما كشش سطحی چیست و چه اهمیتی دارد؟
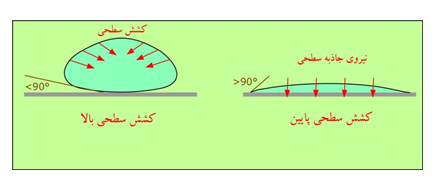
كشش سطحی آب نتیجه به هم پیوستگی مولكولهای آب به یكدیگر از یک طرف و به هم پیوستگی مولكولهای سطحی آب به مولكولهای داخلی آب از طرف دیگر است و یا میتوان گفت نیرو یا فشار داخلی است که مانع از پخش شدن مایع روی سطح می شود.
برای درک بهتر به ذکر آزمایش می پردازیم تا میزان کشش سطحی در مایعات مختلف را با هم مقایسه کنیم. آب به محض اینکه روی سطحی صاف مثل شیشه ریخته شود، معمولاً به صورت قطرات ریز در سطح شیشه پخش میشود، اما الکل به محض ریختن روی شیشه کاملاً پخش شده و تمام سطح شیشه را می گیرد.
حال اگر جیوه (کاملاً مراقب باشید چون جیوه سمی خطرناک است) روی سطحی شیشهای ریخته شود، به هیچ عنوان پخش نخواهد شد و به صورت قطره یا قطرات بزرگ جیوه روی شیشه جمع می شود. در این آزمایش ساده و با توجه به شکل زیر تفاوت سه محلول را در پخش شدن متوجه شدیم. حال محلولی لازم داریم که دارای خاصیت کشش سطحی پایین باشد تا به محض اینکه روی سطح پلیت قرار گرفت تمام سطح پلیت را بپوشاند؛ بنابراین لازم است اگر از آب شهری استفاده می کنیم کشش سطحی آن را تقریباً 72N/m2 کاهش داده و به یک مقدار استاندارد برسانیم تا سطح پلیت در کمترین زمان کاملاً توسط مایع پوشانده شود.
نمودار زیر وضعیت کشش سطح آب را با اضافه شدن افزودنی کاهنده کشش سطحی نشان می دهد. بهترین مایع برای کاهش دادن کشش سطحی آب، الکل است که این مایع می تواند کشش سطحی آب را از ۷۲ به ۴۰ برساند.
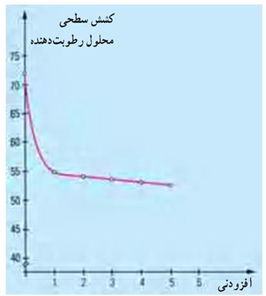
الکل می تواند کشش سطحی آب را کاهش و ویسکوزیته آن را بالا ببرد، جالب است بدانید زمانی که کشش سطحی به ۴۰ برسد، دیگر افزودن الکل تغییری در کشش سطحی ایجاد نخواهد کرد.
آب معمولاً دارای کشش سطحی 72din/cm است. میزان افزودن مجاز الکل به آب برای رسیدن به نتیجه مطلوب بین 5 تا 8 درصد است.
با همه این مواردی که ذکر شد، افزودن الکل به محلول رطوب زنی دارای مزایا و معایبی است که در ذیل به آن ها می پردازیم.
اما ابتدا به مزایای الکل می پردازیم:
- کاهش کشش سطحی: همانطور که ذکر شد عامل مهمی برای سرعت در رسیدن به چاپ مطلوب است.
- افزایش ویسکوزیته محلول: با افزایش ویسکوزیته، انتقال آب و پیوندها افزایش یافته و انتقال به پلیت سریع تر و روان تر انجام می شود.
- کاهش کنداکتیویته (هدایت الکتریکی) در ادامه به تشریح آن خواهیم پرداخت.
- کاهش زمان آمادهسازی چاپ: مسلماً هر چقدر محلول افست سریع تر روی پلیت پخش شود، پلیت سریعتر آماده چاپ شده و اولین نسخه چاپی مطلوب زودتر حاصل می شود، کما اینکه گاهی به دلایل مختلف از جمله عدم ناسازگاری داروی آب و مرکب یا به دلیل کیفیت پایین داروی آب زمان آمادهسازی چاپ که همان مدت زمان رسیدن به چاپ مطلوب است، افزایش پیدا کرده و باطله نیز افزایش مییابد.
- ۵- افزایش کیفیت چاپ: در چاپ افست که بنا بر تضاد آب و چربی بنا شده هر چقدر مناطق تصویر و غیر تصویر بهتر و سریع تر از هم جدا شوند، کیفیت چاپ و تصویر بالاتر خواهد بود؛ بنابراین در صورت استفاده از محلولی که ما را بتواند به این مهم برساند، مطمئناً به یکی از عوامل افزایش کیفیت چاپ دست پیدا کردهایم.
- امکان تغذیه لایه نازک تر محلول روی پلیت: همان طور که ذکر شد با افزودن الکل یا مایع کاهنده کشش سطحی به آب، محلول افست سریعتر در سطح پلیت پخش خواهد شد، اما این پخش شدن اگر به صورت لایه نازکتر باشد، در کیفیت چاپ تأثیر بسزایی دارد؛ چرا که این لایه محلول پخش شده روی پلیت در نهایت به سطح کاغذ منتقل خواهد شد و رطوبت هم سبب تغییر در ابعاد الیافهای کاغذ چه طول و چه عرض خواهد شد؛ بنابراین در نهایت ابعاد کلی کاغذ را تغییر داده و دراصطلاح، کاغذ دفرمه میشود و این به هم ریختن ابعاد استاندارد کاغذ سبب عدم تطابق و رویهمخوری رنگ در چاپهای بعدی خواهد شد. حال هر چقدر این لایه نازک تر باشد، میزان خیسشدگی کاغذ کمتر خواهد بود، کما اینکه یک قانون کلی در چاپ افست می گوید برای تنظیمهای ابتدایی به منظور چاپ همیشه از آب کمتری استفاده شود.
۷-واضح بودن تصویر: هر چقدر ترامهای تصویر کاملاً از هم منفک شوند، در نهایت تصویر وضوح بیشتری خواهد داشت و این مهم توسط داروی آبی که همه مناطق غیر تصویر را میپوشاند، انجام خواهد شد؛ چرا که اجازه ورود مرکب به مناطق غیر تصویر را نمی دهد.
۸-کاهش باطله: همانطور که در قسمتهای قبلی ذکر شد، این مزایا سبب کاهش باطله در ابتدا و در حین چاپ می شود که این مزیت در کنار مزیت افزایش کیفیت، جزو مهم ترین مزایایی است که می تواند برای استفاده از الکل برشمرد.
۹-خاصیت ضد باکتری: الکل مایعی است که کاربردهای فراوانی را می توان برای آن برشمرد از جمله:
۱-می توان به عنوان سوخت از آن استفاده کرد.
۲-به عنوان کاهش دهنده کشش سطحی استفاده کرد.
۳-خشک کننده
۴-ضدعفونی کننده: در چاپ نیز می توان از خاصیت دیگر الکل علاوه بر کاهشدهنده کشش سطحی یعنی خاصیت ضدباکتری آن استفاده کرد تا از ایجاد و افزایش قارچ در محلول جلوگیری کرد.
۱۰-ضد کف: کف ایجاد شده در مخازن محلول در دستگاههای چاپ افست در چاپ اخلال ایجاد کرده و سبب میشود عملیات مرطوبسازی سطح پلیت به خوبی انجام نشود و ایجاد مشکل کند. این موضوع موجب افت کیفیت چاپ می شود، حال الکل با خاصیت ضد کف خود سبب ناپایداری حباب های ایجاد شده می گردد و از ایجاد کف جلوگیری می کند.
۱۱-خنک کننده سطح پلیت: مایعات برای تبخیر نیاز به حرارت دارند و با جذب حرارت تبخیر می شوند؛ بنابراین با تبخیر خود حرارت را از محیط حذف می کنند، حال هر چقدر مقدار مایع بیشتر باشد، میزان جذب حرارت بیشتر و در نتیجه خنکسازی سطح بیشتر خواهد بود. دمای محلول افست حاوی الکل به واسطه تبخیر سریع الکل کاهش پیدا می کند، دمای مطلوب در آبسردکن دستگاه بین ۱۵- ۱۰ درجه سانتی گراد می است.
۱۲- انتقال آب کمتری به سطح کاغذ
- همه خصوصیاتی که ذکر شد در مورد الکل خالص است و در صورتی که الکل ناخالص مورد استفاده قرار بگیرد، هیچ کدام از مزیتهای نام برده شده بدست نخواهد آمد.
اما از معایب الکل می توان به موارد زیر اشاره کرد:
- سبب سایه آوردن کار می شود؛ چون محلول آب به درون مرکب وارد می شود.
- درصد بالای الکل عناصر چسبنده مرکب را با اختلال مواجه می کند.
- در چاپ مرکبهای متالیک،الکل پوشش سطحی پیگمنت های متالیک را حل کرده و درخشندگی را کاهش می دهد.
- الکل می تواند روی پوشش کاغذ تأثیرگذاشته و موجب چسبیدن پوشش کاغذ روی لاستیک شود.
- قابلیت اشتعال بالا (در ۱۲۰ درجه سانتیگراد)
- آلودگی زیست محیطی بالا برای آزاد کردن ترکیبات ارگانیک فرار و تخریب لایه های جوی
- هزینه و قیمت بالا
- سرعت تبخیر بالا سبب کاهش دما و همچنین کاهش میزان الکل و تناوب در اضافه کردن الکل
- ایجاد كف در سیستم رطوبتدهی
- كم شدن عمر لاستیک
- تخریب نوردهای لاستیكی
- برای سلامتی انسان مضراست.
- به دلیل تبخیر سریع ایزوپروپیل مرکب نیز سریعتر خشک میشود و همزمان برج های چاپ نیز به دلیل تبخیر خنک میشوند.
- اثر الکل حداکثر ۲۰درصد است و افزودن بیش از آن اثری در کاهش کشش سطحی ندارد.
آزمایش خلوص الکل
یک لیوان تمیز را به میزان مساوی از آب و الکل پر کرده، بعد از ۳۰ تا ۴۵ دقیقه مایع باید شفاف باشد، کدر شدن الکل نشانه نامرغوب بودن الکل و نامناسب بودن برای دستگاه است.
برای اینکه از مقدار الکل موجود در محلول خود آگاه شوید، می توانید از چگالیسنج استفاده کنید. چگالیسنج میله شیشهای مدرج سادهای است که ته آن یک حباب شیشهای قرار دارد که با قرار دادن چگالیسنج در محلول چگالی آن محلول در سطح خاصی از آن قرار میگیرد. ایزوپروپیل الکل سبب سایه آوردن کار می شود که این کار به دلیل وارد شدن محلول آب به درون مرکب مشکل را دو چندان می کند.
کنداکتیویته (هدایت الکتریکی)
«برای سنجش داروی آب دو فاکتور مهم وجود دارد که باید در هر بار مصرف آب اندازهگیری شود. یکی میزان پیاچ آب است و دیگری هدایت الکتریکی آب که با هدایتسنج کنترل میشود. هدایت الکتریکی به معنای مقدار یونهایی است که در داخل آب وجود دارد که میتواند ناشی از داروی مصرفی و یا وجود هر جسم خارجی در آب باشد. هدایت الکتریکی اگر از حد مطلوب بالاتر باشد به این معناست که محلول رطوبتدهی آلوده است و باید تعویض شود و اگر از حد مطلوب کمتر باشد به معنای رقیق شدن صمغ موجود در داروی آب است و چاره آن بالا بردن درصد دارو است».
اما هدایت الکتریکی چیست؟
رسانایی الکتریکی در واقع مقدار عددی میزان انتقال الکتریسیته در هر محلول است. بر خلاف مواد جامد، رسانایی یک محلول بر تعداد یونها(فلزات باردار) موجود در آن محلول بستگی دارد. تعداد یونها هم به نوبه خود بستگی به مقدار و نوع نمکهای حل شده در محلول دارد. از این رو رسانایی یک محلول بستگی به رطوبت زنی به آب مصرفی و آب داروی اضافه شده به آن دارد.
میزان رسانایی محلول رطوبتزنی تأثیر مستقیمی بر کیفیت چاپ افست ندارد بنابراین نمی توان همانند پیاچ برای آن محدوده مجاز خاصی را در نظر گرفت. با وجود این، توصیه می شود رسانایی محلول رطوبت زنی هیچ گاه بیشتر از sµ ۱۵۰۰ نباشد. این عدد از نسبت محلول و رسانایی محلول بدست میآید.
رسانایی بیشتر یعنی نمک بیشتر و نمک بیشتر نیز سبب خوردگی بیشتر قطعات ماشین چاپ میشود.
- کنداکتیویته (هدایت الکتریکی) میزان عبور جریان الکتریسیته از مایع را نشان می دهد كه واحد آن زیمنس است.
- میزان رسانایی آب ۴۰۰ میكروزیمنس است كه نشاندهنده قابلیت هدایت الكتریكی آن است.
- رسانایی الكتریكی رابطه مستقیم با سختی دارد؛ یعنی هر چه رسانایی بالا برود سختی نیز به همان میزان افزایش می یابد.
- میزان هدایت الکتریکی آب خالص صفر است.
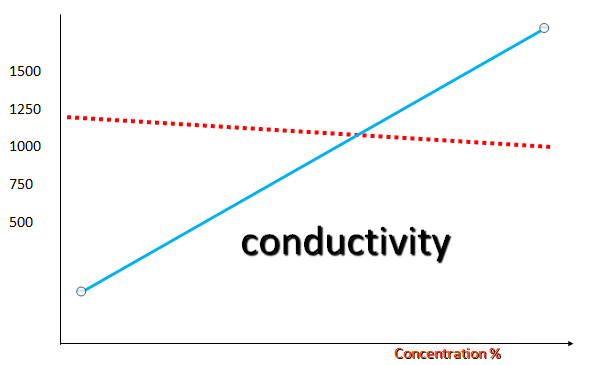
مواد یونی که داخل آب حل میشوند(ناخالص های آب) سبب افزایش هدایت الکتریکی می شود. از این پارامتر برای اندازه گیری کیفیت آب استفاده می شود.
- دما، هدایت الکتریکی را تغییر می دهد.
- با افزایش الکل رسانایی کاهش پیدا می کند.
- هدایت الکتریکی مطلوب ۷۰۰ الی ۹۰۰ میکرواهم است.
- رابطه بین هدایت الکتریکی و میزان مصرف داروی آب خطی است.
- از طریق کنترل میزان هدایت الکتریکی آب ماشین می توان به راحتی قدرت داروی آب و میزان مصرف آن را مشخص کرد.
- به منظور کنترل دقیق شرایط آب ماشین افست و محاسبه مقدار نرمال داروی آب مورد نیاز برای ماشین، تغییرات پیاچ و کنداکتیویته را بر اساس افزایش درصد داروی آب رسم کرده و محل تلاقی دو نمودار، درصد نرمال داروی آب برای مصرف را نشان می دهد.
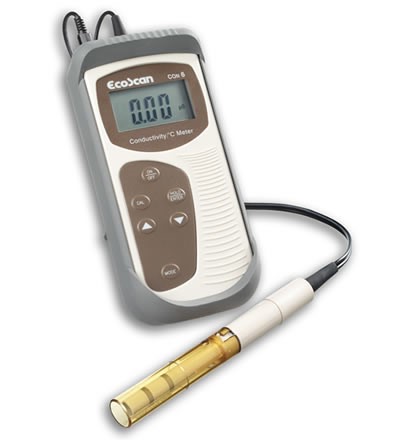
رابطه رسانایی و مقدار آب داروی اضافه شده به محلول رطوبت زنی
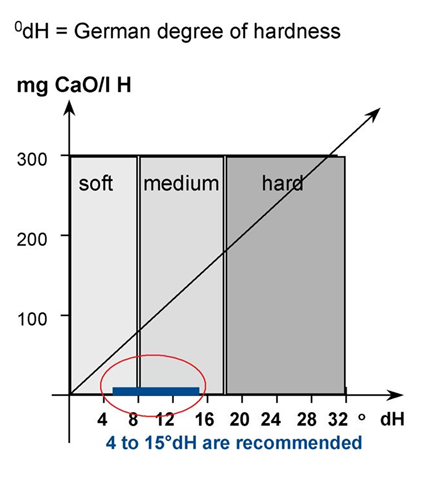
مقدار رسانایی، نسبت مستقیم با مقدار آب داروی موجود در محلول رطوبت زنی دارد. بنابراین می توان بر اساس مقدار رسانایی، مقدار و قدرت آب داروی موجود در محلول رطوبت زنی را محاسبه کرد.
البته باید دقت داشت آب مصرفی نیز رسانایی خاص خود را دارد که میبایست آن را نیز در نظر گرفت (فقط رسانایی آب مقطر خالص تقریباً صفر است). رسانایی محلول رطوبت زنی به شدت به مقدار الکل مصرفی و اجزای حل شده، کاغذ و مرکب چاپ بستگی دارد. از این رو محاسبه مقدار آب داروی لازم برای تهیه محلول رطوبت زنی می بایست در ابتدای شروع چاپ و با نسبت الکل مشخص انجام شود.
مقدار آب داروی لازم برای هر آب مصرفی و نوع کاغذ و مرکب چاپ متفاوت است. برای بدست آوردن این نسبت می توانید با عرضهکننده آب داروی مصرفی خود مشورت کنید.
- مواد یونی که داخل آب حل می شوند (ناخالصیهای آب) سبب افزایش هدایت الکتریکی می شود؛ بنابراین می توان از این پارامتر برای اندازه گیری کیفیت آب استفاده کرد.
امولسیون مرکب
امولسیون در چاپ و نقش آن در کیفیت چاپ
سیستم چاپ افست بر اصل جدایی آب و چربی است و این دو هیچگاه با هم ترکیب نمیشوند، مگر اینکه با اضافه شدن یک ماده امولسیفایر در محلول رطوبتدهی و یا مرکب، این دو ماده با یکدیگر واکنش دهند.
«از نظر تئوری آب و جوهر نباید با هم واکنشی داشته باشند. اما در چاپ لازم است این دو ماده با هم ترکیب شوند. از نظر شیمیایی اگر چربی به شکل قطرههای ریزی درآید، قابلیت حل شدن در آب را داراست که به آن امولسیون میگویند و نمونه بارز آن شیر است».
اگر فرض بر این داشته باشیم که امولسیونی در چاپ صورت نگیرد و مرکب نتواند قطرات آب را جذب خود کند، مرکب به مناطق تصویردار نمیرسد و در نتیجه در چاپ با پدیده کوری (چاپ نشدن قسمتهای تصویردار) رو به رو خواهیم شد.
میزان امولسیون آب و مرکب، قطر قطرات آب امولسیون شده و پایداری امولسیون از جمله عوامل مهم در کیفیت چاپ است. بنابراین توانایی داروی آب در بالانس عوامل فوق سبب افزایش کیفیت، کاهش پرت و مشکلات چاپ می شود.
برای اینکه با اصطلاح امولسیون در چاپ بیشتر آشنا شویم بد نیست نگاهی تخصصی از نظر چاپ به این پدیده فیزیکی داشته باشیم و هم اینکه تأثیر آن را در چاپ بیشتر درک کنیم.
در فرایند چاپ لازم است تعادل میزان محلول رطوبت و مرکب رعایت شود. این مفهوم در چاپخانه ها به امولسیون مصطلح است و حاکی از آن است که مرکب های چاپ، محلول رطوبتدهی را جذب می کنند تا به حالت ثابت و پایدار خود درآیند.
امولسیون بالا موجب اختلالات زیر میشود:
- تنپلات غیر یکنواخت
- چاقی ترام
- پشت زدن
- مانع از جذب مرکب به کاغذ
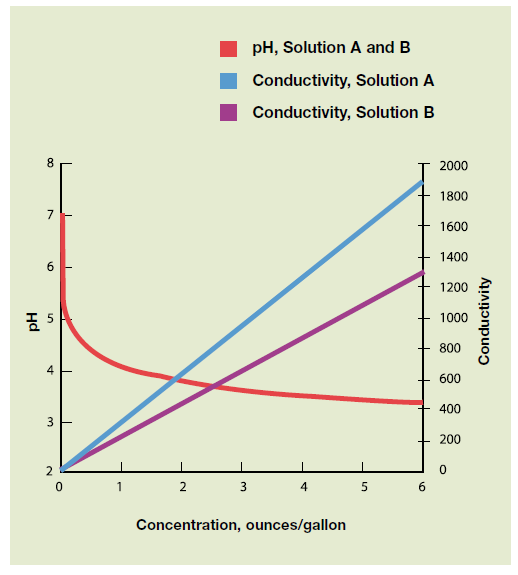
امولسیون وقتی اتفاق می افتد که دو مایع را که نیروی مؤثر بین آن ها فوق العاده زیاد است، بخواهیم با هم مخلوط کنیم؛ نتیجه این خواهد بود که یکی از این دو مایع روی یک مایع دیگر به صورت قطرات پخش می شود. محلول مرطوب کننده از طریق زینک و نوردهای مرکب روی فرم به قسمت مرکبدان انتقال پیدا می کند و یک حالت امولسیون را با مرکب به وجود می آورد.
محلول مرطوبکننده به نسبت ۲۰ تا ۲۵درصد روی مرکب پخش می شود. معمولاً مرکب های با قدرت جذب ۳۰درصد آب در بازار عرضه می شوند.
این یک تصور غلط است که فکر کنیم برای دستیابی به چاپ بهتر باید مواد افزودنی قوی به آب اضافه کنیم، این محلول سبب ایجاد امولسیون معکوس میشود. مخلوط آب و مرکب در مرکبدان ایجاد امولسیون ناپایدار می کند پس هر کار چاپی را ابتدا باید با استفاده از کمترین مقدار آب ممکن شروع کرد.
نشانه های عدم بالانس مناسب آب و مرکب:
۱-شناور شدن مرکب در تشتک آب
۲-رطوبت زیاد یا براق بودن زینک
۳-پاشش مرکب روی گاردها، کف و بدنه
۴-رنگ ها یکدست نیستند و از نظر دانسیته مرکب و کمرنگی و پررنگی هم یکدست نیستند.
۵-رنگ ها کم حال به نظر می رسند و دانسیته کمی در پوشش مرکب وجود دارد.
- ترام ها مرکب کافی نمی گیرند.
۷-آسیب دیدن جزئیات سایه های بخشی از تصاویر.
از آنجایی که تمام مرکب های چاپ باید با محلول مخزن، امولسیون تشکیل دهند سطح تشکیل امولسیون در چاپ بایستی کنترل شود.
چگونه یک بالانس آب و مركب صحیح داشته باشیم؟
مراحل زیر باید بهعنوان دستورالعمل برای تنظیم بالانس آب و مركب در دستگاه چاپ شما اعمال شود.
- در یک لحظه در هر یونیت سطح آب به میزان ۵ درجه كاهش می یابد؛ بنابراین ۳۰ تا ۵۰ دقیقه اجازه دهید دستگاه چاپ واکنش نشان دهد.
- به سطح مركب نگاه كنید و تا اندازه ای كه تراكم میزان مركب مناسب را بدست آورید، سطح مركب را كاهش دهید.
- این مراحل را تا زمان رسیدن به حداقل تنظیم آب ادامه دهید، زمانی كه زمینه كار كثیف به نظر می رسد و تراكم مركب در حد مورد نظر ما یا كمی پایین تر است، آن زمان ما حداقل تنظیم را خواهیم داشت.
- اگر كار چاپی زمینه آورد، كمی سطح آب را بالا بگیرید.
- زمانی كه تنظیم آب به حالت مناسب رسید، اقدام به تنظیم مركب برای رسیدن به چاپ مناسب بكنید.
مزایای بالانس آب و مركب مطلوب:
- زمانی كه میزان آب و مركب در كمترین سطح است، تنظیمات مركب در كل چاپ یكدست و بدون نوسان است.
- رویهم خوری رنگهای تنپلات بهبود پیدا می كند. مثلا تنپلات ماژنتا و قرمز، قرمز بهتری را نتیجه خواهد داد.
- در چاپ چهار رنگ، ما شاهد چاپ بهتری خواهیم بود.
- كاهش ایجاد پرز روی لاستیک سیلندر.
- ضعیف شدن زینک كم می شود.
- هزینه كمتر، باطله كمتر و در نتیجه تولید بیشتر
- كاهش مالیدگی مركب
- كاهش تشكیل لایه مركب روی نوردهای هدایت كاغذ
- پشت زدن كمتری خواهیم داشت.
- چاقی ترام كمتر.